An efficient backup generator for a solar system
C-Lab Home
Here at C-Lab, we run mainly from solar power, with plans to add wind
and hydro someday. Any reasonably designed solar power system
needs a backup generator of some kind, at least if you want 100%
reliability. The cloudy days of February are just too numerous to
have enough panels and batteries to run a business from them alone,
although this would be plenty for my (Doug's) personal use, given that I
don't have to do heavy power consumption when there's not much
available. Most backup generator solutions are heiniously
inefficient, with electricity from those sources often costing more than
$2 per KWH, once you include replacing the prime mover (gasoline engine)
every so often.
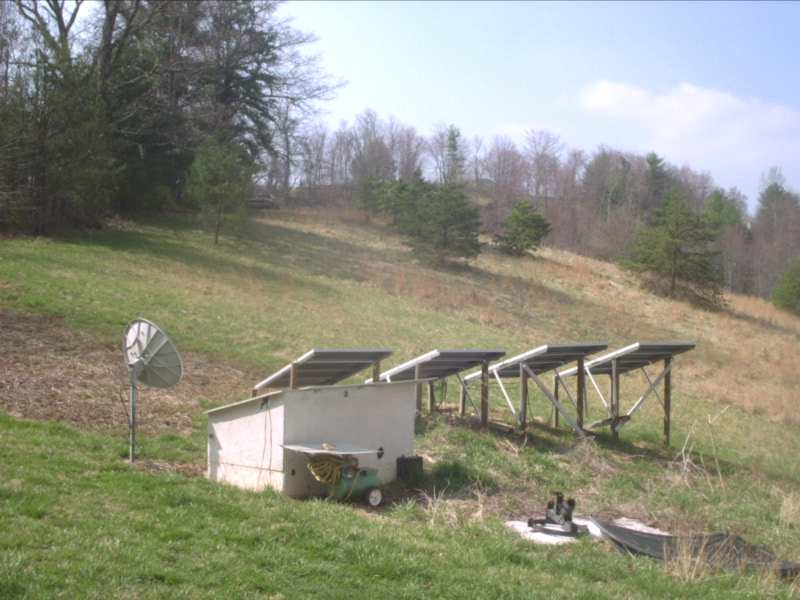
The above is our system as it sits currently. The dish is our
internet satellite uplink, from Starband.
The shed contains the batteries, electronics, and generator.
Wiring back to the office is buried. The disassembled C band dish
on the lower right will be converted for two uses, a radio telescope,
and a solar concentrator using aluminized mylar as the reflector.
If you have a solar system, you know that keeping your batteries in
good shape is the main thing you worry about. Cycling them nearly
100% of capacity shortens their life considerably, as does letting them
sit around in a low state of charge. However, when charging them,
you can't just pour the coals to them, you must do so at a reasonable
rate or other bad things happen. Thus, making a good battery
charger is a non-trivial exercise.
For background, here's the basic system. We have 16 120 watt
Solarex polycrystaline panels, 12 375 Ah 6v batteries hooked up as a 24v
bank, a Cruising Systems solar charge controller, and a Trace SW 4024
inverter. All of this is outdoors, the batteries and major
electronics are in what we call the energy shed, a 4 ft tall 4 by 8 ft
little building with a roof that hinges up in segments and side doors
for access to things. That's just the business, my house has it's
own system and they can back one another up. One bay of the energy
shack holds a fairly unique and very efficient backup generator.
Deep-cycle lead-acid batteries don't like to be charged much faster
than C/10, which means it would take a 10 hour period to charge them
from dead to full. In practice, as they near full charge, you
cannot go even that fast without boiling the electrolyte furiously,
which is a bad thing. It wastes energy converting water to
hydrogen and oxygen, releases corrosive sulfuric acid fumes, and
requires that you put in water to replace the loss. I've never
seen contamination fall _out_ of
a battery during that last process! Most charge controllers taper
off the charge when the batteries get to about 70% full to avoid these
bad things. However, an internal combustion engine has nearly the
same frictional and other losses no matter what the load on it is, so
the charger system built into most inverters is terribly wasteful.
You wind up running an internal combustion engine at full speed but
light load for hours to put that last little bit of charge in.
Here we decided to sidestep many of these problems by sizing a
generator so it could run flat out all the time until we achieved about
80% charge on the batteries, similar in concept to how a properly
designed hybrid automobile should work. AC generators are
intrinsically a problem here, as they have to run (usually) at 3600 rpm,
which is the power peak of most small engines, but not the torque peak,
which is where the efficiency peak is, at least under heavy load.
In other words, this is optimized for "Brake-specific fuel consumption".
Thermodynamic efficiency rises with increasing compression ratio, which
is why diesels are popular for some applications. However, they
stink (literally) and fuel is hard to get without the road taxes (lots
of paper work, each time, versus once a year for the gasoline on my tax
form). So we decided to go with gasoline power -- in a pinch, say
if we are snowed in, we can siphon fuel from the car. The highest
compression ratio small engines available are from Honda, and these have
proven in decades of testing here to also be by far the most reliable. So
our prime mover is chosen. Now for the generator part. We
don't want to make AC in a cheezy aluminum winding generator
(ugh). We just want to charge batteries at 22-30 volts DC.
Surplus Center in Nebraska sells various DC generators which are war
surplus from WWII. We were lucky to find a pair of 200 amp 24v
generators from P51 airplanes (and others) that are built like the
proverbial tank. Now, we don't need the full 200 amps here, as our
battery bank capacity is about 1100 Ah total. This is good, as
these generators have very little frictional loss, and sure don't mind
running at about half capacity. They don't even get warm, which
would increase the loss resistance of the solid copper windings.
Copper has a pretty large temperature coefficient of resistance, so
running hot is a no-no.
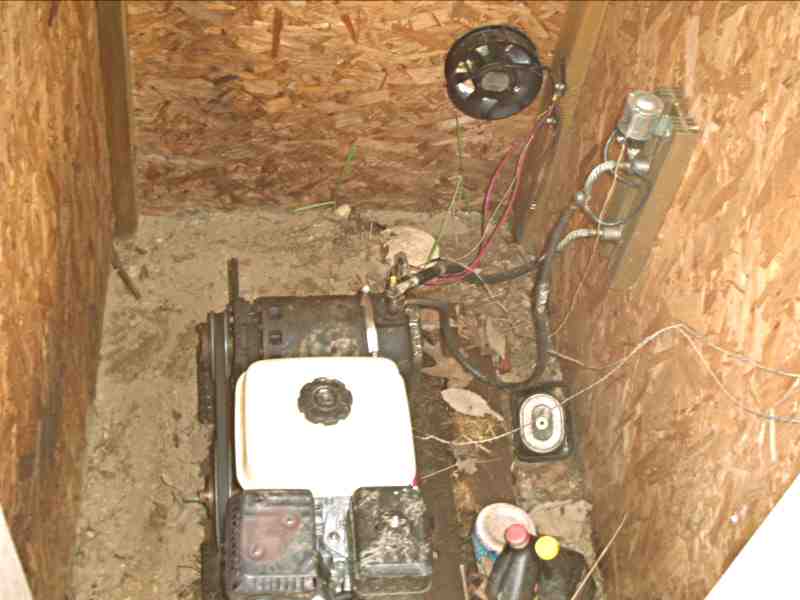
In the picture, you can see the actual surplus generator, the 24v
cooling fan, the coupling diode on a heatsink, the starter solenoid, and
the field resistor (mounted by fan, red wires). And, oh yes, the
mess one accumulates in a few years runtime. The wires trailing
off to the right go to the start/stop buttons. We have, in the
past, made these remote-start. This was a bad move. It's
much better to force the user, even us, to at least look at the thing
before starting it. Not having a big remote gas tank ensures this
as well. Failures in the past have included trying to start a
motor that was hydro-locked due to a piece of grit getting into the
float valve, filling the engine and crankcase with gasoline, and putting
the rest of the bulk tank on the ground. A 1000 amp fuse blew,
luckily without igniting the gas! It's better to enforce some sort
of inspection each time, one catches the odd loose bolt or bad belt
before vibration damage that way.
One interesting event has caused a panic failure. A lightning
bolt struck about 100 feet away, and shorted out one of the two diodes
you see mounted on that heatsink. This caused the generator to try
to start, sans gas, and a frantic effort to go unbolt one of the wires
to stop it, all while it was live. Brushing the terminals with a
wrench creates quite the shower of sparks! Things like this of
course always happen during bad weather. When you are your own
power company, you have a job that sometimes needs to be done right now,
like it or not.
To make a long story short, a lot of putzing around established that we
wanted a 7" pulley on the 5.5 hp Honda motor and a 4" pulley on the
generator, so that we could run the Honda at it's most efficient RPM and
the generator the same. Larger pulleys are better than smaller, as
at around 5hp, you are pushing the torque a V belt can transmit. A
massive approximately 2 ohm resistor made from part of an old electric
dryer heating element (thanks Dad!) handles the field current
setting. This was adjusted until with the Honda throttle wired
wide open, we got the best current and fuel efficiency -- running the
Honda at its torque peak, rather than at maximum horsepower. In
our application, even with "no sun", about 3/4 gallon a day (about 2
hours of runtime at roughly 100 amps output) of gasoline is consumed to
run a rather large computer network, complete with color laser printer,
satellite internet uplink, chemistry and physics labs, machining, and
anything else our engineers think they need to play with. Of
course there is rarely "no sun", the panels even respond measurably to
the full moon, but some days it gets awful dark in the mountains, and
instead of getting the nominal 50 amps from the panels (limited by the
controller) we get more like 5, enough for a private person to keep the
stereo on, but not enough to run a consulting business.
This design has been refined for decades, and is now "ready for prime
time" to be sure. It just works. We have electric start via
the generator itself using a starter solenoid, automatic cuttoff via a
programmable relay in the inverter, and "it just works".
The biggest things in getting here were learning that the commercial
grade Briggs/Techumsa sorts of small engines just don't hack it, small
or cheap pulleys don't hack it, and vibration is your biggest enemy to
long life otherwise. (Grainger for the pulleys, the kind with the
separate hubs) We've had the Briggs or other small engines need a
new exhaust valve at only 300 hours of runtime, and be completely worn
out at twice that, a bad joke, fine for lawnmowers maybe, but not for
real hard useage. I've got one Honda that has over 10,000 hours of
runtime on it, but retired it to my logsplitter to put a newer one in
the more important service. Vibration problems have been solved
two different ways. One was to bolt the generator base to a large
chunk of concrete, but that only lasted about 7 years, as the concrete
couldn't really take it -- and now I have a 700 lb chunk of useless
concrete in the backyard. The current setup has four 2 foot long
pieces of 9/16" rebar driven directly into the earth and welded with
huge welds to the generator base. This seems to do a better
job. Don't even consider vibration isolation mountings. They
are designed to protect other
stuff from the vibration of whatever is mounted on them, not the mounted
stuff itself, which now has an even worse vibration/acceleration
problem. Without some sort of stiff mounting like this, things
start work-hardening and rattling/breaking off, and even the 1/4" thick,
angle iron reinforced mild steel base isn't immune to this. BTW,
at some point in the process we learned that Havoline straight 30 weight
oil is the stuff to use, we got double the life out of many motors we've
tested with it. Too bad they recently sold their lubricants
division, I hope the quality stays high. Slick 50 is also well
worth it in the small quantities needed. Remember, what we have
here is essentially a dyno, so we can actually see the improvments when
friction is reduced. We see from 7-10% here when things are
fresh. No word on lifetime improvements with the Slick 50, as the
current lashup hasn't had to run anything like 10,000 hours yet, that
takes many years. We have a lot of solar panels now, after all,
which wasn't the case earlier on. Chalk that up to taking cash in
lieu of stock options during the dot boom, a wise decision in retrospect.
Tuning V belt type and length is important to life of all the
parts. If the belt gets into "whipping" it generates huge
vibrations and side torques on the various bearings, a bad thing.
This is especially bad for the Honda's crankshaft seals, which will
start to spin in the casting and leak oil if severely abused.
Currently the best we've found is an oversize V belt used in Simplicity
Legacy tractors for running the PTO. These last seemingly forever
compared to "extra good" belts from the tractor supply store, and have
low losses otherwise. I've yet to find a generic supplier for
these, but since I have one of the above mentioned tractors, I have "hot
spares" available, and worn belts from the tractor work fine for
this. Basically, the design uses the shortest practical V
belt. This is to keep the overall size down as well as reduce
whipping. A little length adjustment is provided for via slots in
the generator mounting. It's rarely needed however, as the glory
of the V belt (the good you get in exchange for accepting their other
sins) is that they pull themselves down into the V of the pulley when
torque is applied. Generally, when it's time to adjust, it's time
to replace it anyway.
Did I mention, that in the usual C-Lab way, this was cheaper to build
and to operate than anything normally commercially available? The
reliability is awesome, and this thing will start in sub-zero
temperatures even without using the choke. The generator, used as
a starter motor, simply cranks the thing so fast it will warm up quickly
from friction and oil viscosity (the same thing) and then start.
Even "dead by solar system standards" batteries will crank this just
fine, but of course you could always pull the cord. Once started,
the solenoid is released and a 400 amp diode on a heatsink carries the
current to the battery bank. This is a safety issue -- I'd love to
get rid of the diode losses. An older system used a latching
solenoid, but what if the engine shuts down (or tries to) due to low
oil, no fuel, and so forth? This puts the generator back into
motor mode, drawing about 200 amps and the only symptom is the slight
change in noise level. You can imagine that this only happens when
the weather is terrible and it's in the middle of the night on a
Saturday (no parts available till Monday), and you would not be far off.
Doing this "off the grid" thing has been quite humbling. When I
first "cut the soles off my shoes, moved to the mountains and learned to
play the flute" I thought I was hot stuff. After all, I had
designs both in orbit and under the poles -- the government was a nice
employer early in my career. Well here, it's just different.
You don't design things that will never break, that's
impossible/impractical in this enviornment. You design things that
rarely break, but are easy to fix in a sleet storm with stuff you have
laying around on a Sunday night. 'Nuff said.
Re: the advantages of being off the grid.
There are a couple of silver linings not often mentioned. I have
one solar system that has experienced zero failures in nearly 20 years
of operations. You "5 nines" guys can eat your hearts out.
The business has had a single planned one second failure to switch to
the new system in nearly that long. Talk about reliable, most
other things, especially including the power company, aren't even in the
same league as this system. The ultimate UPS.
The other silver lining I put up with some trepidation. If you
don't have "power company" power, you are effectively considered a
"disaster area" by the government, and your house, buildings, and
business are considered essentially worthless for tax purposes.
This affects the ROI in significant ways.
C-Lab Home